Tech
A chemical claw machine bends and stretches when exposed to vapors
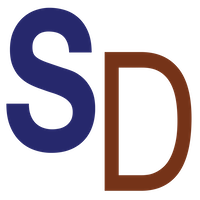
Scientists at King Abdullah University of Science and Technology (KAUST) in Saudi Arabia have developed a tiny “claw machine” that is able to pick up and drop a marble-sized ball in response to exposure to chemical vapors.
The findings, published July 12 in the journal Chem, point to a technique that can enable soft actuators — the parts of a machine that make it move — to perform multiple tasks without the need for additional costly materials. While existing soft actuators can be “one-trick ponies” restricted to one type of movement, this novel composite film contorts itself in different ways depending on the vapor that it is exposed to.
“It can bend and stretch depending on molecular interactions, which is very sophisticated at this size range,” says author Niveen M. Khashab, a Chemistry Professor at KAUST. “We hope our findings will be used to develop advanced soft robotic systems capable of precise and adaptable movements in various environments,” she says, suggesting the systems could be used in medical devices, industrial automation, and tools used to measure temperature, air quality, and humidity.
To test the claw machine’s ability to perform multiple tasks, the researchers first exposed it to acetone. In the presence of this vapor, the device gripped a red cotton ball and stretched so that it could drop it in a box. When the team exposed the machine to ethanol vapor, it grabbed the cotton ball and removed it from the box.
Unlike rigid actuators in “hard robots,” which may be made from metal or tough plastic, soft actuators are flexible, enabling them to perform a range of tasks their rigid counterparts cannot. As a result, soft actuators have been the technology of choice for cutting-edge applications such as precision agriculture, deep-sea exploration, and wearable devices.
But soft actuators are still limited — they can either bend, twist, or stretch, but no one actuator can move in multiple ways, preventing them from performing more complex tasks that would lend them to an even greater range of uses. While researchers have recently experimented with actuator designs to give devices a greater range of motion, many of these strategies involve combining different materials, which makes them costly and difficult to manufacture while increasing their risk for mechanical failure.
To overcome this challenge, Khashab and colleagues developed a claw machine made from a polymer matrix containing molecular cages with the organic compound urea. The researchers chose urea for the cages because the compound can form multiple hydrogen bonds, allowing the urea molecules to rapidly reconfigure when they are exposed to different molecules in vapors. As a result, the material’s properties can be precisely controlled, making it easy to customize.
The findings suggest that the material the machine is made from can be “effectively programmed to achieve complex movements by judiciously controlling the type and the concentration of the vapor stimulus,” the authors write.
“The most remarkable finding was the unique actuation behavior where the soft actuator performed a complex motion involving ‘curvature, stretching, and reverting,’ which had not been reported previously,” says Khashab.
Next, Khashab and colleagues plan to study the claw machine’s energy density and how efficiently it converts energy so that they can enhance its performance, she says. They will also test its ability to produce electrical signals when the soft actuator is combined with materials that generate an electric charge, with the ultimate goal of developing flexible wearable electronic devices, says Khashab.
This work was supported by the King Abdullah University of Science and Technology (KAUST).